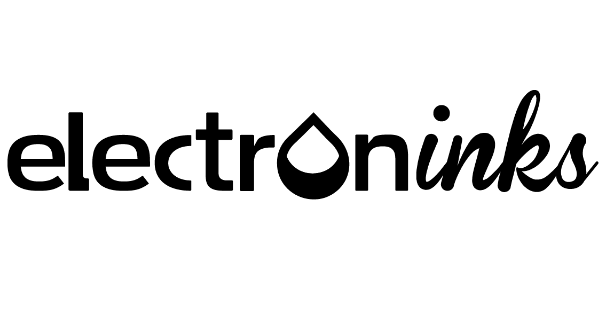
Electroninks, Inc., today announced the production-scale availability of its full suite of proprietary metal organic decomposition (MOD) conductive metal ink solutions. In addition to bringing standalone ink products to market, Electroninks is also bringing total solutions to the customer with its line of ink products, including its own small (desktop) prototype additive manufacturing solution for rapid on-demand printed circuit board (PCB) printing and repair, called CircuitJet.
Based on Electroninks metal-complex chemistries, these materials are often referred to as “particle-free” inks due to their translucent nature. Being particle-free is a paradigm shift in technology compared to conventional nanoparticle inks and pastes that, to date, have been the main option for metallization in printed electronics. This chemistry, inspired by precursors used in vacuum deposition techniques and now built into printed inks, provides product designers and manufacturers of virtually any hardware device an entirely new palette of electronic materials for printing high-performance circuitry, accelerating time to market for new innovations, reducing costs, and increasing sustainability in the metallization process.
Now with full production scale availability of its solutions, Electroninks is well positioned to meet the needs of global commercial customers through its new world-class 30,000-square-foot R&D and production facility in Austin, Texas. The company is already serving a select set of commercial customers in the display and semiconductor packaging supply chains, as well as acting as a key supplier for the U.S. Department of Defense (DoD), including the U.S. Air Force.
“Traditional conductive inks and metal deposition methods have been around for decades, but are slow, problematic, expensive, and not at all environmentally friendly,” said Brett Walker, co-founder and CEO, Electroninks. “Our metal complex particle-free inks radically change the game. They’re our secret sauce and set a new standard for conductive inks in 21st century electronics manufacturing.”
Electroninks currently offers an array of silver, gold and platinum-based inks in their MOD platform, with others (including nickel and copper in prototyping phase). These ink technologies generally fall into three product lines:
CircuitShield™: Low maintenance ink products for EMI Shielding and back-end semiconductor metallization. CircuitShield powers the technology that produces smartphones with 5G capabilities. Dramatically reducing capital expenditures, CircuitShield eliminates spray nozzle clogging, residue in silver film, and provides high shielding effectiveness. With long shelf-life and excellent printing stability at room conditions, CircuitShield results in key advantages compared to PVD, with almost no ink maintenance, a much lower cost of ownership, the ability to setup rapid prototype design, and much lower equipment footprint. It is used for 5-sided SiP shielding with aspect ratio from the top to the side wall close to 1. Other use-cases involve wafer metallization and conformal via coating. CircuitWrap™: Ink products used as bezel/wrap electrodes in touch panel displays, and micro/miniLED panels. With exceptional electrical, mechanical, and reliability performance in a <2um thickness film, CircuitWrap is the go-to product for customers in display and touch panel and can be patterned down to <3um Line/Space. This results in an ideal material for bezel electrodes in touch panel (and foldable touch panels), wrap electrodes in micro/miniLED panels, and metal mesh films for flexible display technologies. Electroninks’ particle-free ink technology allows for a seamless deposition onto patterned substrates that will then be metallized to create a fine metal mesh - perfect for the thinnest and most flexible of displays. Panel-makers and OEMs in OLED, micro/miniLED can produce foldable touch-screens for displays ranging in size from sets, to mobile, to AR/VR lenses. CircuitSeed™: Thin, dense films used as 3D/finely patterned seed layers for subsequent metallization by plating. A radically more efficient method for plating electronics – reducing a 20-plus step process to a few steps and using at least 40 times less water and substantially less energy. A low-cost, agile solution, it supports multiple chemistries that can be printed via a variety of techniques as dense, finely patterned seed layers on surfaces ranging from rigid to flexible plastics, and even 3D.
Electroninks invested considerable resources to carefully partner with key equipment providers such as inkjet, aerosol jet and screen printers, so its ink products can be handed off in tandem with best-in-class printing technology.
“We have worked very closely with our high-value strategic partners and collaborators in the name of providing our customers what they need – as close to a turnkey product as possible," said Melbs LeMieux, co-founder and President, Electroninks. “Our brand of conductive ink technology is relatively new to customers, so any further technical and cost-model support we can provide beyond just the ink is key to their adoption to replace conventional nanoparticle pastes and PVD type metallization.”
Rapid on-demand PCB prototyping
Electroninks also announced its own small (desktop) prototype additive manufacturing solution for rapid on-demand PCB printing and repair, called CircuitJet. CircuitJet enables customers that need very fast PCB prototyping on up to an 8x10 form factor with a simple “all-in-one” tool that retails for under $5,000 USD.
Designed for 21st Century Manufacturing
Designing and manufacturing circuit boards using traditional subtractive etch processes is costly, time consuming, and not practical for today’s highly wired world. CircuitJet, CircuitSeed, CircuitShield, and CircuitWrap eliminate the need for traditional deposition methods while simultaneously enhancing the production of an array of applications that require high-quality materials at lower costs. From electronic and mobile displays, rigid PCBs, and medical devices to electromagnetic shielding and e-textiles, Electroninks’ solutions meet the needs of a wide range of manufacturers.
The traditional subtractive design and manufacturing process uses more material which generates additional waste, adding to environmental challenges. Electroninks’ solutions are additive: they use 3-D printing technology to add layer upon layer of metal ink to create miniaturized circuitry. This manufacturing process reduces costs, waste and decreases production time.
All of the company’s products are available for immediate use in high-volume, production scale applications, and can also be customized according to customer specifications as needed. Please visit Electroninks Products for more detailed information and technical specifications for all solutions.